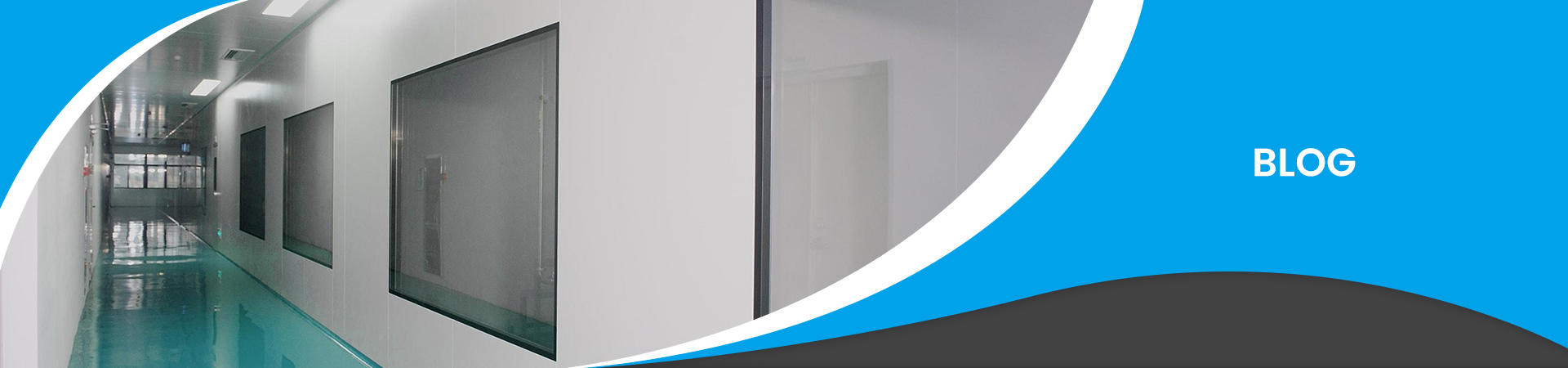
What Are Cleanroom Doors Typically Made Of?
- By:Lisa
- 2025-07-22
- 29
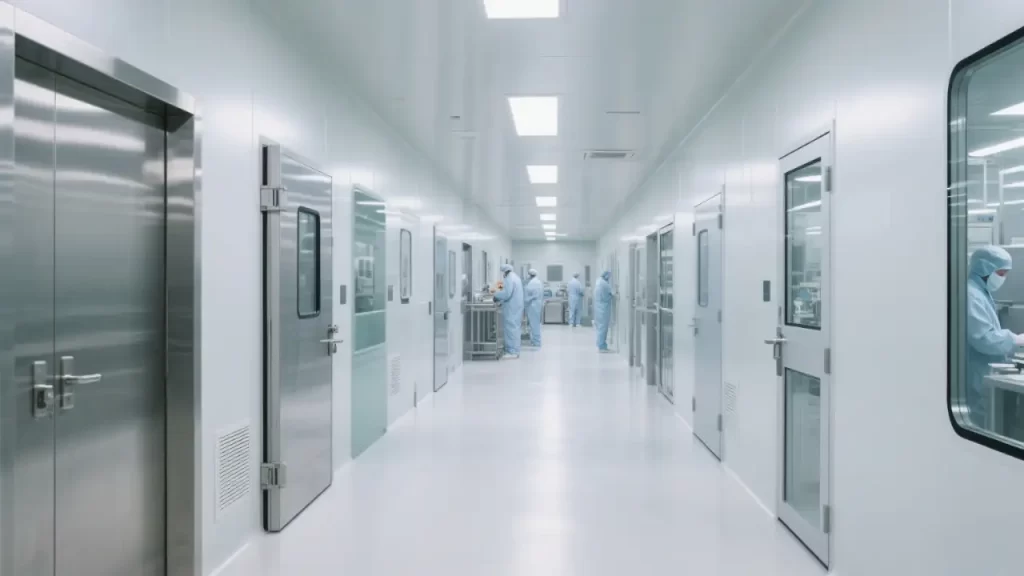
Cleanroom doors play a pivotal role in ensuring a pristine, contamination-free environment for industries like pharmaceutical manufacturing, electronics, and biotechnology. These specialized doors are engineered to meet rigorous cleanroom standards, such as those defined by ISO 14644-1 (e.g., ISO 5 to ISO 8), which set limits on airborne particulate levels. For instance, an ISO 5 cleanroom allows no more than 3,520 particles of 0.5 micrometers per cubic meter. Selecting the right cleanroom door material is crucial for airtightness, durability, and adherence to Good Manufacturing Practice (GMP), all while minimizing the risk of cross-contamination. This article dives into the materials used in the construction of cleanroom doors, their benefits, and how they align with specific cleanroom requirements to maintain a sterile environment and boost operational efficiency.
Why Is Choosing the Right Material for Cleanroom Doors So Important?
The material of a cleanroom door directly affects its ability to ensure the integrity of a clean environment. These doors must provide robust door seals to prevent contaminant ingress and maintain room pressure—for example, ISO 5 cleanrooms require a positive pressure of 25–50 Pa, per EN 12207 standards. In pharmaceutical settings, doors need antimicrobial surfaces that are easy to clean to withstand rigorous cleaning protocols. In electronics, antistatic materials are essential to safeguard sensitive equipment. Choosing the wrong material can lead to contamination, failure to meet FDA regulations (e.g., 21 CFR Part 211), or costly production shutdowns.
Key factors in door selection include:
- Cleanroom Classification: ISO 5 demands top-tier door seals to prevent air leakage, while ISO 7-8 allows more cost-effective options.
- Industry Needs: Pharmaceutical manufacturing prioritizes sterile surfaces, while electronics requires antistatic properties.
- Environmental Conditions: High humidity or chemical exposure calls for durable materials.
- Maintenance Costs: Long-lasting materials cut down on repair and replacement expenses.
By selecting the right cleanroom door, you enhance contamination control, ensure compliance, and create a clean environment that supports maintaining a sterile environment and prevents airborne contaminants.
Common Materials for Cleanroom Doors
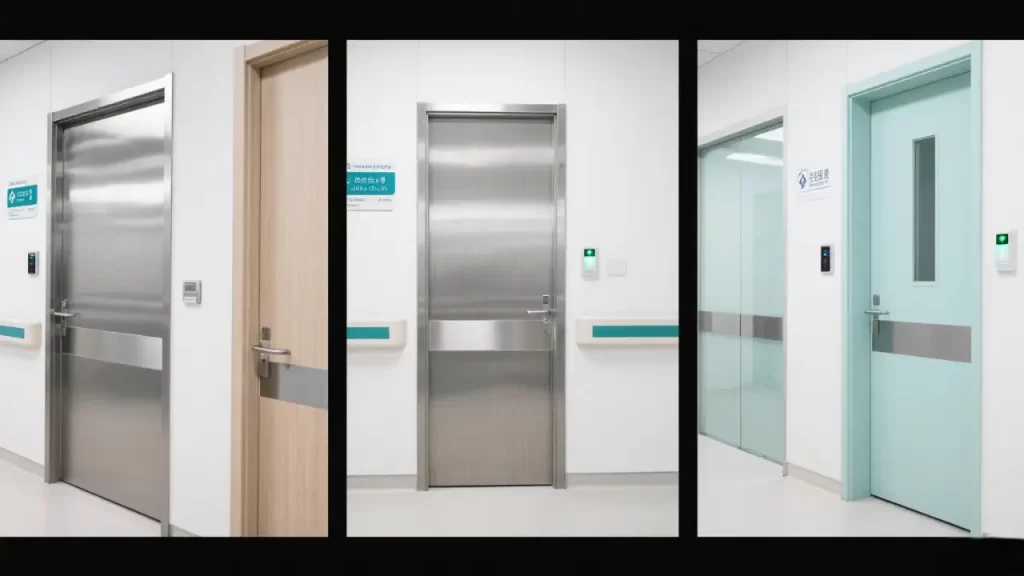
1. Stainless Steel (304 or 316L)
Stainless steel is a go-to material for cleanroom doors thanks to its unmatched durability and corrosion resistance.
Advantages:
- Stands up to acidic disinfectants (pH 2–12), perfect for high-traffic pharmaceutical cleanrooms.
- Built to last, with a lifespan of 15–20 years (ASHRAE testing).
- Easy to clean, with a smooth surface (Ra<0.8μm) that resists bacterial growth (ISO 22196).
Drawbacks:
- Higher cost ($500–$800 per square meter).
- Heavier, requiring sturdy door seals and framing.
Applications:
- Pharmaceutical facilities and operating rooms, compliant with GMP for ISO 5–6 cleanrooms.
2. Aluminum (6061-T6 Alloy)
Steel or aluminum—specifically aluminum—is prized for its lightweight and budget-friendly qualities in modern cleanroom settings.
Advantages:
- Lightweight (2.7 g/cm³), making door operation and entry and exit smoother in high-traffic areas.
- Anodized for corrosion resistance, ideal for humid environments.
- Cost-effective ($300 per square meter).
Drawbacks:
- Lower tensile strength (310 MPa vs. 500 MPa for stainless steel), less suited for high-impact areas.
Applications:
- Semiconductor manufacturing and modular cleanrooms, designed to meet ISO 7–8 standards.
3. High-Pressure Laminate (HPL)
HPL is an affordable, non-porous material for cleanroom doors.
Advantages:
- Ultra-low surface porosity (<0.1%), reducing contamination control risks (ISO 22196).
- Antimicrobial, wiping out 99% of surface bacteria.
- Budget-friendly ($200 per square meter).
Drawbacks:
- Less resistant to strong acids.
Applications:
- Pharmaceutical and food processing cleanrooms (ISO 7–8).
4. Tempered Glass
Tempered glass doors blend practicality with aesthetics in cleanroom environments.
Advantages:
- 90% transparency for easy monitoring, boosting operational efficiency.
- High impact strength (250 MPa, ANSI Z97.1).
- Sleek, modern look that doors enhance.
Drawbacks:
- Heavier (25 kg/m²) and pricier ($400–$600 per square meter).
Applications:
- Semiconductor observation areas and labs (ISO 6–7).
5. Fiberglass Reinforced Plastic (FRP)
FRP excels in chemically harsh cleanroom environments.
Advantages:
- Resists acids and alkalis (pH 1–14).
- Lightweight (1.8 g/cm³), minimizing footprint stress.
- Customizable to meet the required specifications.
Drawbacks:
- Weaker impact resistance.
Applications:
- Chemical labs and battery production (ISO 7–8).
6. Vinyl or PVC-Coated Materials
Vinyl or PVC coatings provide superior airtightness for cleanroom door designs.
Advantages:
- Air leakage rate <0.1 m³/h (EN 12207), ensuring cleanroom pressure stability.
- Cost-effective ($150 per square meter).
- Versatile for door functions like swing doors, sliding cleanroom doors, or bi-parting doors.
Drawbacks:
- Shorter lifespan (5–8 years).
Applications:
- Biotechnology labs needing a sterile environment (ISO 5).
Factors Influencing Material Selection
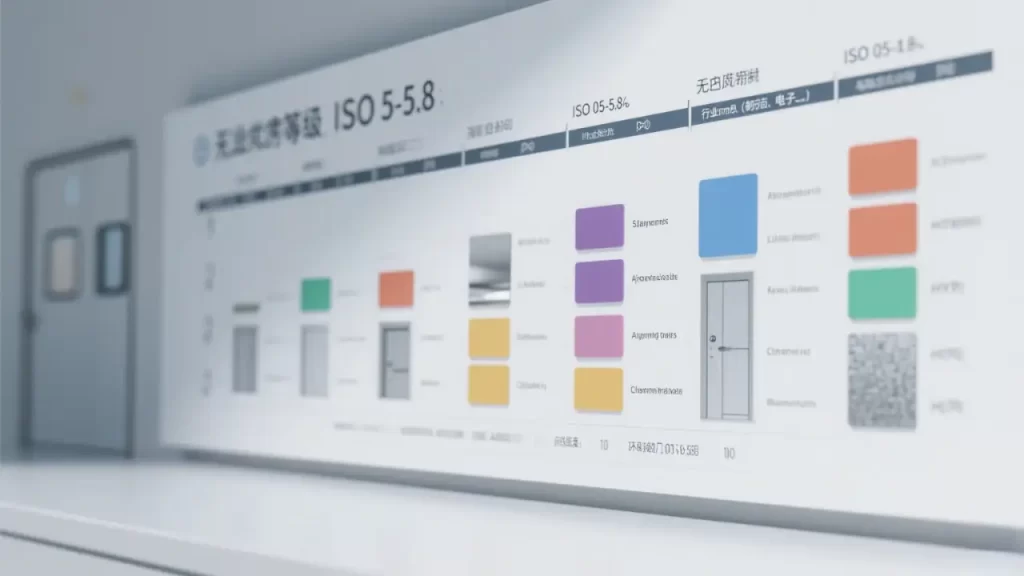
Selecting the right cleanroom door material requires weighing several factors:
- Cleanroom Classification: ISO 5 demands door seals to prevent cross-contamination, while ISO 7–8 allows more economical choices.
- Industry Needs: Pharmaceutical cleanrooms need antimicrobial materials; electronics require antistatic properties.
- Environmental Conditions: High humidity or chemical exposure calls for using materials like FRP or stainless steel.
- Budget and Maintenance: HPL or PVC suits budget-conscious projects, while durable materials lower long-term costs.
Cleanroom doors are equipped with features like interlocking systems or automatic doors to minimize airflow disruptions and ensure ease of access. For instance, sliding cleanroom doors or roll-up doors save space and reduce airborne contaminant risks in high-traffic areas. In the event of a fire, some doors include special features to ensure the integrity of the cleanroom.
Benefits of Choosing the Right Cleanroom Door Material
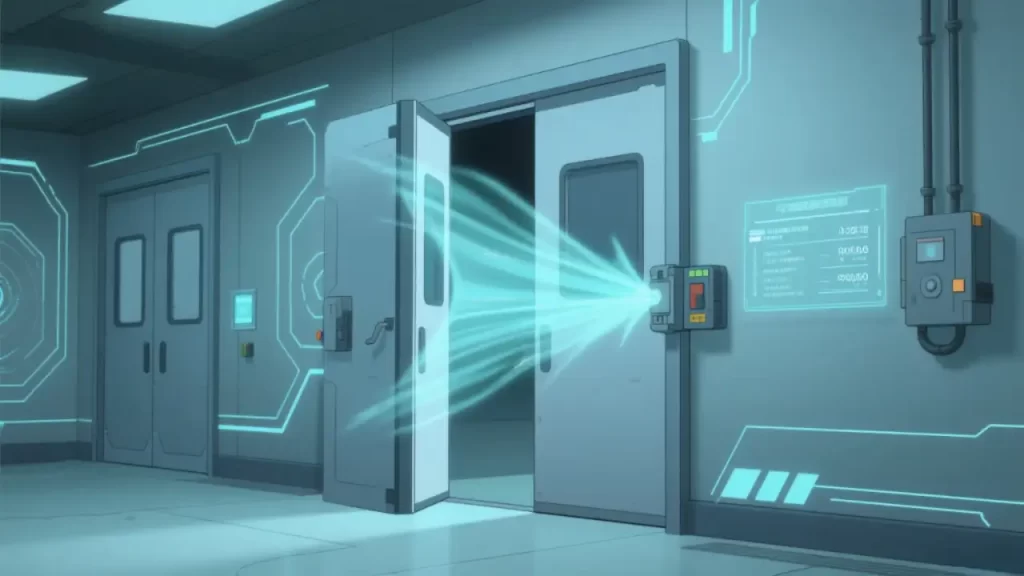
The appropriate door material strengthens contamination control with non-porous surfaces that prevent microbial growth, critical for pharmaceutical and biotechnology cleanrooms. Stainless steel and HPL are compliant with FDA regulations, ensuring cleanroom compliance. Durable materials like stainless steel or FRP reduce maintenance costs, offering long-term savings. Door functions like automatic doors or interlocking systems in swing doors or bi-parting doors optimize airflow and cleanroom pressure, enhancing operational efficiency. Ultimately, the right door plays a key role in maintaining a sterile environment, preventing contaminant ingress, and upholding the integrity and functionality of the cleanroom.
Conclusion
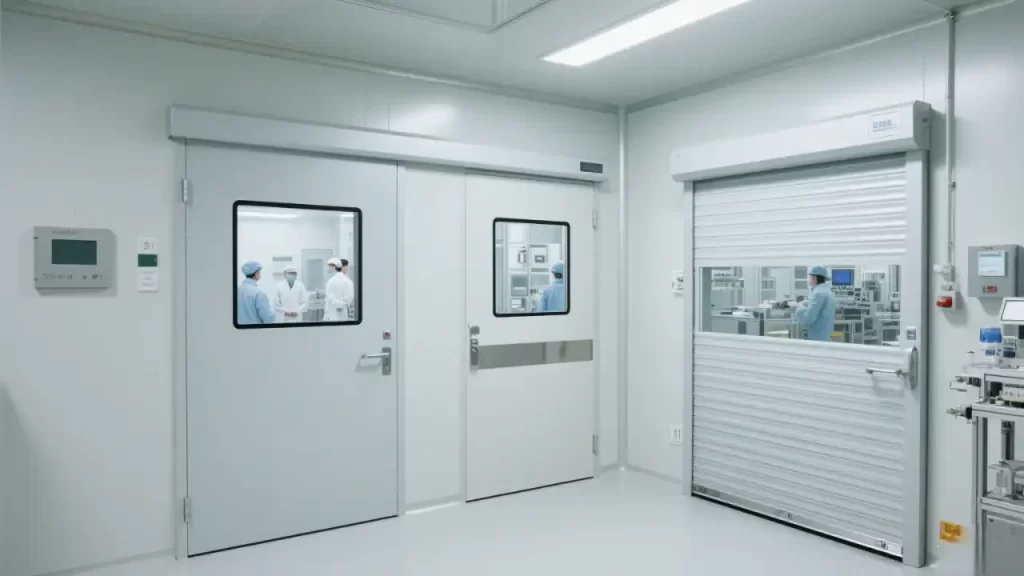
Cleanroom door selection is critical for maintaining a sterile, clean environment. Stainless steel is ideal for pharmaceutical ISO 5–6 cleanrooms, while steel or aluminum and HPL suit ISO 7–8 settings. Tempered glass offers visibility, and FRP and PVC address specific needs. Doors are built to align with ISO standards, industry requirements, and environmental factors, ensuring contamination control, compliance, and operational efficiency. Whether using swing doors, sliding cleanroom doors, or roll-up doors, cleanroom doors offer robust door solutions that minimize air leakage, meet specific cleanroom requirements, and maintain the level of cleanliness needed for efficient, compliant operations.
-
Cleanroom Glass Windows Are The Key to Maintaining a Clean Environment
-
Top Aluminium Profile Manufacturers in China: Leading the Global Market
-
The Evolution of Air Tight Sliding Doors
-
AHU Aluminium Profile: A Comprehensive Guide
-
The Importance of Choosing the Right Cleanroom Door in Vietnam
-
The Benefits of Hospital Automatic Doors: Enhancing Efficiency and Safety
-
The Best Bathroom Door Manufacturers - Unlocking Endless Possibilities!
-
Unlock the Possibilities with AJ Manufacturing Doors
-
Make a Statement with Manufactured Home Interior Doors!
-
what is aluminum profile? Aluminum Profiles for Your Home is the best option
-
Cleanroom Design Mistakes and How to Avoid Them
-
What Are Cleanroom Doors Typically Made Of?
-
High Speed Clean Room Doors Cut Contamination Risk
-
Dustproof Cleanroom Door Innovation for Sterile Spaces
-
How Cleanroom Half Glass Swing Door Enhances Sterile Access
-
Why Custom Cleanroom Aluminum Profile Matters Today
-
Smart Ceiling Air Diffuser: Dampers Add Full Control
-
E-ZONG: Trusted Air Tight Sliding Cleanroom Door Manufacturer
-
Top Benefits of Clean Room Roll Up Door Systems
-
Cleanroom Glass Door Innovations You Should Know
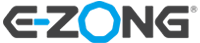
Guangzhou Yizhong Aluminum Industry Co., Ltd.
We are always providing our customers with reliable products and considerate services.
We are always providing our customers with reliable products and considerate services.
Speak Your Mind